By Qiao Dong, Yuan Taoxiong, People's Daily
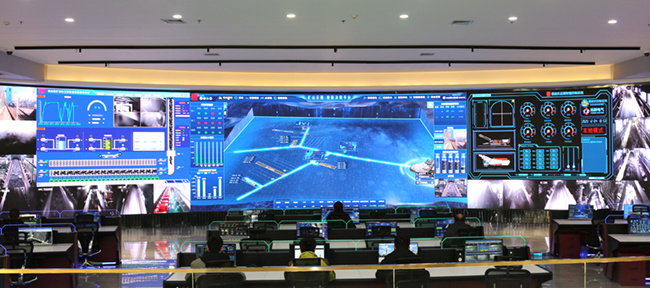
A smart dispatch center of a coal mine of Jinneng Holding Group in Datong, north China's Shanxi province, dispatches vehicles. (Photo from the official website of Jinneng Holding Group)
In recent years, 5G and industrial internet have seeped into the development of China's traditional mining industry, driving the upgrading of the sector and ensuring safe and orderly production. They have injected new impetus into the high-quality development of the mining industry.
Two-hundred meters under a coal mine of Jinneng Holding Group in Datong, north China's Shanxi province, coals are excavated, screened, loaded and transported under the collaboration of multiple devices.
All the work is completed remotely by operators on computers in a ground control center, where a big screen is showing real-time videos of each underground channel and checkpoint, as well as all relevant indicators.
The integration of 5G and industrial internet not only ensures more effective and precise remote control for coal mines, but also significantly improves the efficiency of relevant enterprises' safety inspection.
He Junying is an employee of Bin County Coal Co., Ltd. who works in the Jiangjiahe coal mine of the company in Bin county, Shaanxi province. He received an alert from a smart big data platform the other day that said abnormal vibration was detected on the suspension arm of a coal cutter. He immediately contacted the technology center in Shanghai that's responsible for analyzing the data on the platform, and experts from Shanghai informed him of the analysis result and gave him advice on maintenance via a remote analysis system.
Shaanxi Shengwei Building Materials Group Co., Ltd. developed an intelligent self-diagnosis system at the end of the last year. The system checks devices every five minutes with sensors deployed in places that manual inspection is not able to reach. General manager Wang Yong of the company told People's Daily that 5G and industrial internet have brought immediate changes as the incidence of unexpected machine shutdowns dropped 70 percent after the system was installed, and the maintenance cost has also been cut by 30 percent.
"What really makes inspections smart is real-time monitoring," said Lyu Le, director of 5G technology for energy businesses of China Mobile's Shanxi branch. The company has specifically developed technology of synchronized timing by 5G stations for underground work, which has a precision of less than 100 nanoseconds.
"I had a rough time when I worked as a truck driver in coal mines in the past years, as I had to endure the coldness of winter and the heat of summer," said Li Mingxin, an autopilot truck dispatcher of a cement company under a coal mine group in central China's Henan province. Now the man works in front of a computer in an office building and is able to manage over 20 autopilot trucks just with clicks on the mouse.
"The computers can automatically plan transport routes, and control the trucks via 5G signals," Li said, adding that such approach is highly efficient.
General manager of the cement company Xiao Zhanding introduced that 5G, internet of things and Beidou navigation technologies are advancing the smart construction of coal mines. Tackling human-machine and machine-machine collaboration problems caused by lagged signal transmission, the company has made all mining procedures unattended and controlled remotely, including excavation, transport and monitoring. It has improved both the safety and efficiency of the work.
From unattended operation to automatic monitoring, automated devices are getting more and more synergetic. "Shared data is the key," said Li Shouqing, director of the industrial internet business division under the Shanxi branch of China Unicom.
For instance, all the data of the 18 sub-systems in the Jiangjiahe coal mine is shared in all procedures to conduct real-time monitoring of the operation of each system and the underground environment, and analyze abnormal data, he introduced.
"The analysis result is timely sent to a dispatch center, which has further enhanced the capability of the coal mine of dispatching, emergency handling, and decision making," the director said.
Two-hundred meters under a coal mine of Jinneng Holding Group in Datong, north China's Shanxi province, coals are excavated, screened, loaded and transported under the collaboration of multiple devices.
All the work is completed remotely by operators on computers in a ground control center, where a big screen is showing real-time videos of each underground channel and checkpoint, as well as all relevant indicators.
The integration of 5G and industrial internet not only ensures more effective and precise remote control for coal mines, but also significantly improves the efficiency of relevant enterprises' safety inspection.
He Junying is an employee of Bin County Coal Co., Ltd. who works in the Jiangjiahe coal mine of the company in Bin county, Shaanxi province. He received an alert from a smart big data platform the other day that said abnormal vibration was detected on the suspension arm of a coal cutter. He immediately contacted the technology center in Shanghai that's responsible for analyzing the data on the platform, and experts from Shanghai informed him of the analysis result and gave him advice on maintenance via a remote analysis system.
Shaanxi Shengwei Building Materials Group Co., Ltd. developed an intelligent self-diagnosis system at the end of the last year. The system checks devices every five minutes with sensors deployed in places that manual inspection is not able to reach. General manager Wang Yong of the company told People's Daily that 5G and industrial internet have brought immediate changes as the incidence of unexpected machine shutdowns dropped 70 percent after the system was installed, and the maintenance cost has also been cut by 30 percent.
"What really makes inspections smart is real-time monitoring," said Lyu Le, director of 5G technology for energy businesses of China Mobile's Shanxi branch. The company has specifically developed technology of synchronized timing by 5G stations for underground work, which has a precision of less than 100 nanoseconds.
"I had a rough time when I worked as a truck driver in coal mines in the past years, as I had to endure the coldness of winter and the heat of summer," said Li Mingxin, an autopilot truck dispatcher of a cement company under a coal mine group in central China's Henan province. Now the man works in front of a computer in an office building and is able to manage over 20 autopilot trucks just with clicks on the mouse.
"The computers can automatically plan transport routes, and control the trucks via 5G signals," Li said, adding that such approach is highly efficient.
General manager of the cement company Xiao Zhanding introduced that 5G, internet of things and Beidou navigation technologies are advancing the smart construction of coal mines. Tackling human-machine and machine-machine collaboration problems caused by lagged signal transmission, the company has made all mining procedures unattended and controlled remotely, including excavation, transport and monitoring. It has improved both the safety and efficiency of the work.
From unattended operation to automatic monitoring, automated devices are getting more and more synergetic. "Shared data is the key," said Li Shouqing, director of the industrial internet business division under the Shanxi branch of China Unicom.
For instance, all the data of the 18 sub-systems in the Jiangjiahe coal mine is shared in all procedures to conduct real-time monitoring of the operation of each system and the underground environment, and analyze abnormal data, he introduced.
"The analysis result is timely sent to a dispatch center, which has further enhanced the capability of the coal mine of dispatching, emergency handling, and decision making," the director said.